LCA Case Studies
Although steel is the primary component of hot-dip galvanized steel, there is a significant difference in the environmental performance of hot-dip galvanizing in comparison to other corrosion protection systems. Two major differences between hot-dip galvanizing and other coatings, such as paint, are that HDGs maintenance-free longevity eliminates additional environmental impact during use, and the zinc coating is recycled at the end-of-life. These differences can lead to significant differences in the environmental impact of steel projects, as can be seen in the following case studies.
Balcony Structure
VTT Technical Research, renown for establishing environmental product declarations (EPDs) for building products, conducted life-cycle assessments (LCAs) comparing a hot-dip galvanized balcony to a painted balcony of identical design3. The goal of the study was not only to measure the sustainability of hot-dip galvanized steel, but also to establish a baseline for future improvements. The study demonstrates although the steel comprises the majority of both balconies, the coating is a significant part of the LCA profile.
The environmental assessments of the balconies were based on the following parameters:
- 60-year service life
- 1,715 lbs (778 kg) galvanized steel balcony
- HDG Corrosion Rate: 0.51.0 microns per year (ISO 14713)
- No HDG Maintenance Required
- 420ft2 (39m2) Painted Balcony
- Paint system: zinc-rich epoxy primer (40 microns),
epoxy intermediate (160 microns),
polyurethane topcoat (40 microns) - Paint Maintenance: year 15, 30, and 45 (ISO 12944)
- Paint system: zinc-rich epoxy primer (40 microns),
The environmental impact criteria examined were: primary energy demand (PED), global warming potential (GWP), acidification potential (AP), and photochemical ozone creation potential (POCP). The results show the durability of the coating plays a huge role in the overall environmental impact. The three maintenance-cycles required for the painted balcony account for almost half of the energy requirement for the painted structure, while the galvanized balcony required no additional material or energy inputs. The following graphs illustrate the total PED of each phase of the LCA, the percentage of the PED consumed by the coating, and the GWP, AP, and POCP values.
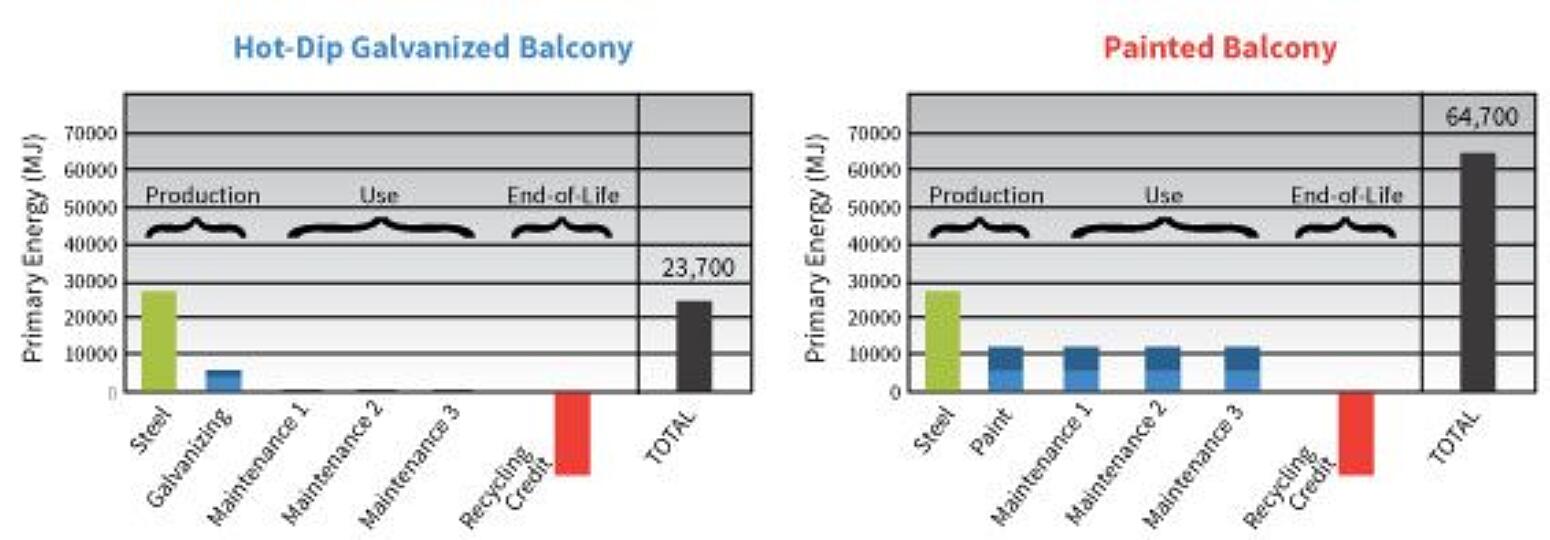
The graphs above show the total primary energy demand (PED) for the hot-dip galvanized balcony is 23,700 MJ (30.5 MJ/kg), or just 37% of the 64,700 MJ (83.2 MJ kg) required for the painted balcony. Keep in mind, if the painted balcony is left in service for even one more year, an additional maintenance-cycle would be required and more energy demand and emissions would be added to the values shown, while the galvanized balcony will remain untouched
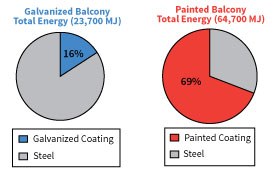
The difference in the energy demand for each balcony structure is even more striking when you consider the percentage of the total energy attributed to the coating. Galvanizing only contributes 16% of the total energy demand, where paint contributes 69% by the end of the 60-year life. According to the study, each paint maintenance cycle consumes an amount of energy equal to that used in the original production, while galvanizing protects the steel throughout the entire 60-year life without maintenance.
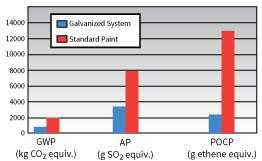
In addition to the energy savings, there are significant differences in GWP, AP, and POCP. For each indicator, galvanizing has a fraction of the environmental impact of the paint coating. This proves that although the coating is a minimal part of the overall sturcutre, there are significant differences in environmental impact.
Parking Garage
The Institute for Environmental Protection Technology at the Technical University of Berlin conducted life-cycle assessments (LCAs) comparing a hot-dip galvanized parking structure to a painted one4. Similar to the VTT Technical Research study, the Technical University of Berlin strived to determine the environmental impact of hot-dip galvanizing as well as establish a benchmark for future improvements. The results of the study demonstrate once again the significant impact the coating plays in the overall environmental impact of the parking garage.
The following parameters were used in the parking structure study:
- 60-year service life
- 1 m2 steel part (20m2/metric tons
- Galvanized coating corrosion rate of 1 micron per year (ISO 1461, C3 environment)
- No HDG Maintenance Required
- Paint system: 3-coat system, 240 microns thick
- Paint Maintenance: years 20 and 40 (ISO 12944)
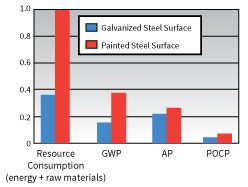
This study also examines the PED, GWP, AP, and POCP values for each system. The results for each impact area are much less for the hot-dip galvanized garage than for the painted one. Similar to the painted balcony, the two maintenance cycles required for the painted garage significantly increase the resource and energy consumption of the painted garage. As galvanizing requires no maintenance during the 60-year life, the total energy and resource consumption for the galvanized structure is only 32% of that required for the painted garage, where the GWP is 38% of paint. Furthermore, the AP is 15% less than paint, and the POCP 33% less.