Durability
Another aspect of hot-dip galvanizing is proven durability. Hot-dip galvanized steel has been specified extensively in petro-chemical, industrial, power/utility, and bridge/highway projects because of its unmatched durability in these harsh environments. Hot-dip galvanizing remains durable thanks to its abrasion resistance, uniform protection, and complete coverage.
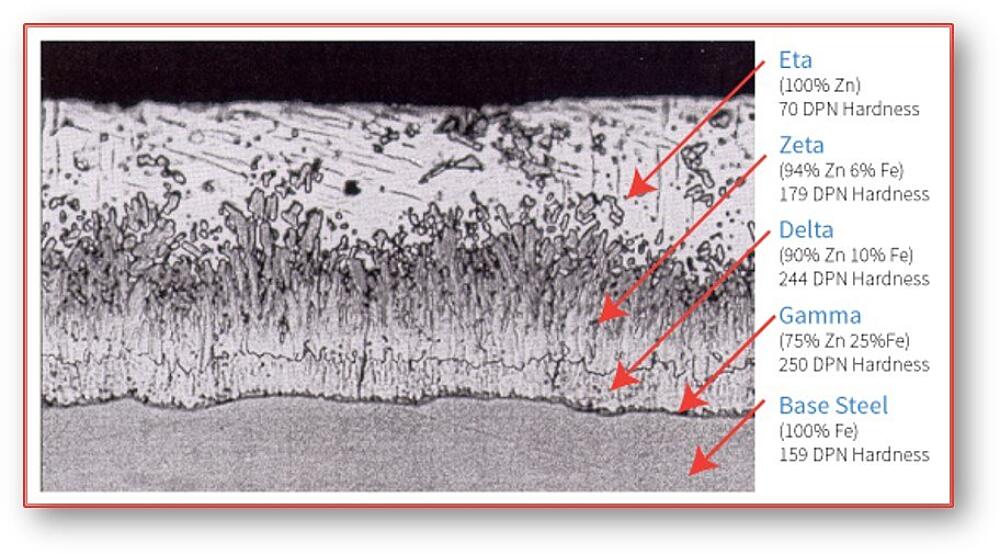
Abrasion Resistance
A unique characteristic of the hot-dip galvanized coating is the development of metallurgically bonded (~3,600 psi), abrasion resistant intermetallic layers. This photomicrograph is a cross-section of a galvanized steel coating showing the three intermetallic layers (Gamma, Delta, and Zeta) and top layer of pure zinc (Eta). During the galvanizing process, these layers develop naturally during a metallurgical reaction between the iron in the steel and zinc in the kettle. As the photomicrograph also shows the hardness of each of the layers as a Diamond Pyramid Number (DPN), you can see the three intermetallic layers are harder than the base steel, while the eta layer has ductility which makes damaging the HDG coating very difficult.
Hot-dip galvanizing’s abrasion resistance provides unmatched protection against damage caused by rough handling during transport and erection, as well as in service. Other coatings with lower bond strengths (300-600 psi) can be easily damaged during shipment and construction, weakening their effectiveness, as barrier protection is dependent upon the integrity of the coating.
Uniform Protection
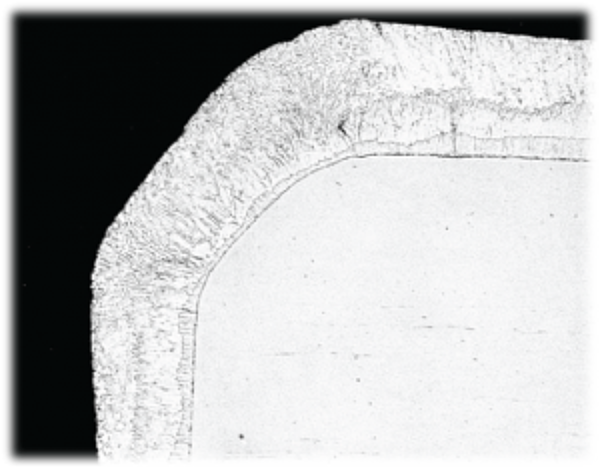
Another aspect of HDGs durability is its uniform protection. During the metallurgical diffusion reaction in the galvanizing kettle, the galvanized coating grows perpendicular to all surfaces. Therefore, the coating is naturally as thick on corners and edges as flat surfaces. Since coating damage commonly occurs at edges, added protection at these junctures is important. Brush- or spray-applied coatings have a natural tendency to thin at corners and edges leaving the part prone to attack. The uniform protection of hot-dip galvanized steel leaves no weak points for accelerated corrosion.
Complete Coverage
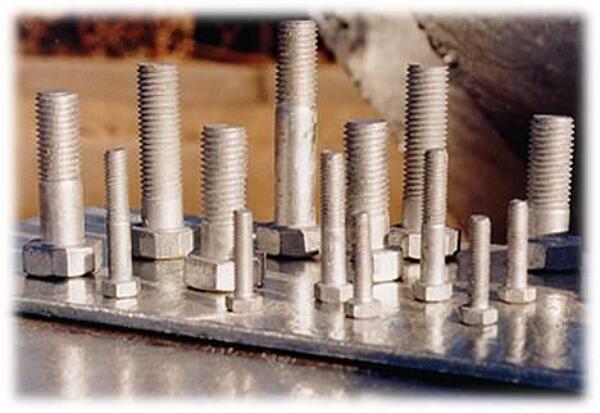
Hot-dip galvanizing is a total immersion process, meaning the steel is fully submerged into cleaning solutions and the molten zinc coating all interior and exterior surfaces. This complete coverage ensures even the insides of hollow and tubular structures and the threads of fasteners are coated. As corrosion tends to occur at an increased rate on the inside of hollow structures where humidity and condensation occur, interior coverage is very beneficial. Hollow structures that are painted have no corrosion protection on the inside. Fully coating fasteners is equally important as they are utilized at connection points which are critical to structural integrity.
Durability Case Study
Cliffwalk at the Capilano Suspension Bridge, Vancouver, BC - 2011
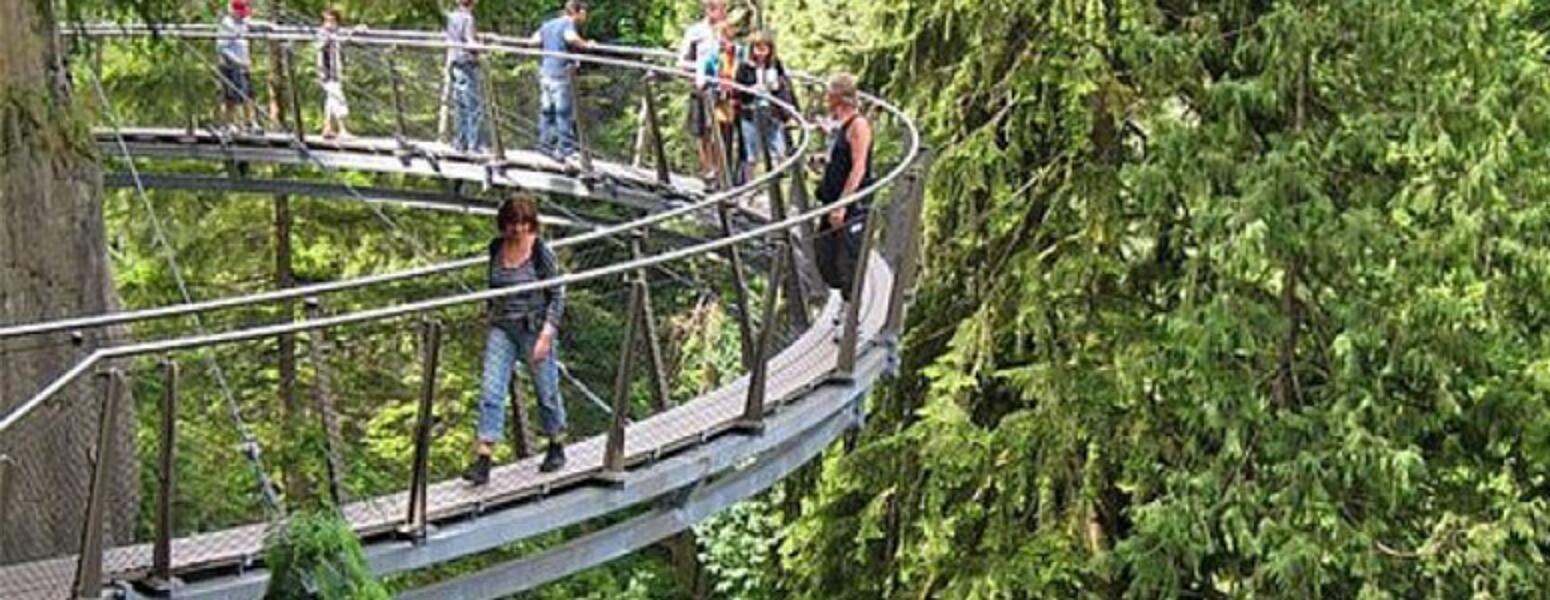
Reaching out over a misty expanse of evergreen foliage, The Cliffwalk at Capilano Suspension Bridge dares visitors to tread out over the open canyon below and drink in the bird’s-eye view. With the Capilano River rushing below the treetops, visitors can fully experience nature’s majesty above, beside, and below.
One of the most popular tourist attractions in British Columbia, the original bridge was constructed in 1889, spanning 450 feet across and 230 feet high. The new Cliffwalk path is just 20 inches wide, with only woven steel and glass siding separating you from the expanse of empty air below.
The Cliffwalk's cliffside location makes it difficult to maintain or repair, as the arc hangs 90 meters above the river below. Furthermore, the attraction is located only a few miles from the Pacific coastline that surrounds Vancouver, making corrosive moisture in constant contact with the exposed steel elements. A maintenance-free corrosion protection system was critical to avoid the dangerous, costly, and unpleasant task of routine maintenance, and the superior barrier and corrosion protection of hot-dip galvanized steel made it the ideal choice to protect this new facility.
Capilano Suspension Bridge’s VP of Operations, John Stibbard came up with the idea while rappelling in Capilano Canyon. Four years and $4.5 million later, the Cliffwalk is designed to serve as a medium for the interactive educational displays developed with the David Suzuki Foundation.
Daring visitors of all ages will see galvanized steel in all corners of the park and the Cliffwalk structure itself. The natural, matte gray aesthetic will blend easily into the cliff face and forest environment. Aesthetics were of key importance to this project, which was intended to feel light and airy.
The strong, durable galvanized steel that comprises the Cliffwalk will keep visitors safe while existing maintenance-free for decades of adventurous visitors to enjoy.