Zinc: The Healthy Metal
Now that you have a solid understanding of structural steel, and its benefits, it is important to understand the other primary component of hot-dip galvanized steel: zinc.
Zinc is a healthy metal that is infinitely renewable without the loss of any physical or chemical properties (just like steel). Approximately 30% of the world’s zinc supply currently comes from recycled sources, and 80% of zinc that can be recycled is (reclamation rate).
More than 13 million tons of zinc are produced annually. Approximately 60% of this is used in galvanizing (sheet and batch), and there are a number of other zinc coatings as well, which will be discussed shortly. However, zinc has many other uses beyond construction, and it’s important to understand some base characteristics about the element, namely, zinc is natural, abundant, and essential to life.
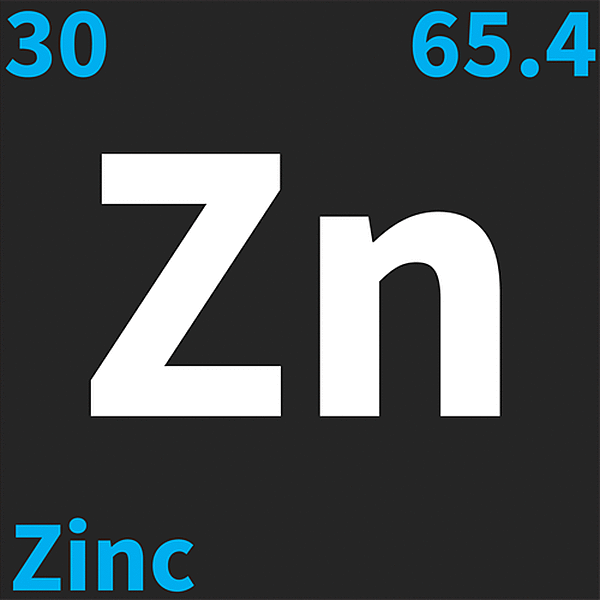
Zinc is Natural & Abundant
Zinc exists naturally in air, water, and soil. Most rocks and many minerals contain zinc in varying amounts. It is the 24th most abundant element in the Earths crust and some 5.8 million tons of zinc are naturally cycled through the environment annually by plant and animal life, rainfall and other natural activity. During the course of evolution, all living organisms have adapted to the zinc in their environment and use it for specific metabolic processes. The amount of zinc present in the environment varies from place to place and season to season.
Zinc is Essential
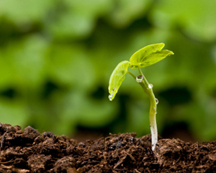
Zinc is essential for all life, from humans to the smallest microorganism Zinc is essential for digestion, reproduction, kidney functioning, breathing, diabetes control, taste, smell, and much more. Although zinc in excess can be detrimental, zinc in deficiency is of far more concern, as the World Health Organization (WHO) estimates 800,000 people in developing countries die each year because of lack of zinc in their diet. Symptoms of zinc deficiency include immune system dysfunction, mental lethargy, vision problems, fertility problems, respiratory and skin allergies, and premature aging.
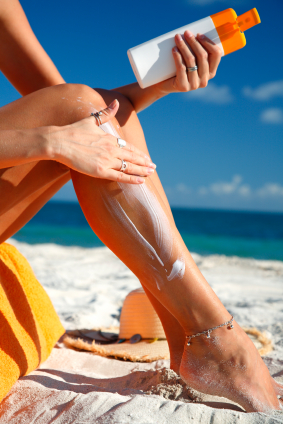
Zinc is Common
Zinc (in oxide or other compound form) is used in a number of products we all use regularly. Zinc is commonly found in sunscreen (remember Zinka from the 80s, the neon colored cream you put on your nose), in fact, zinc oxide blocks more UV rays than any other single ingredient. Zinc is also common in treatment of sunburns, baby creams to prevent diaper rashes, treatment of acne, cold sores, dandruff, treatment of wounds, burns, surgical incisions, cosmetics, and even relief from common cold symptoms.
Other Zinc Coatings
As previously noted, the majority of zinc production goes into construction, namely galvanizing. However, there are a number of other zinc coatings, often called galvanizing, that have their own unique characteristics. It’s important to understand the differences in the coatings, as all zinc coatings are not the same; in fact, their physical, chemical and corrosion resistance characteristics can be extremely different.
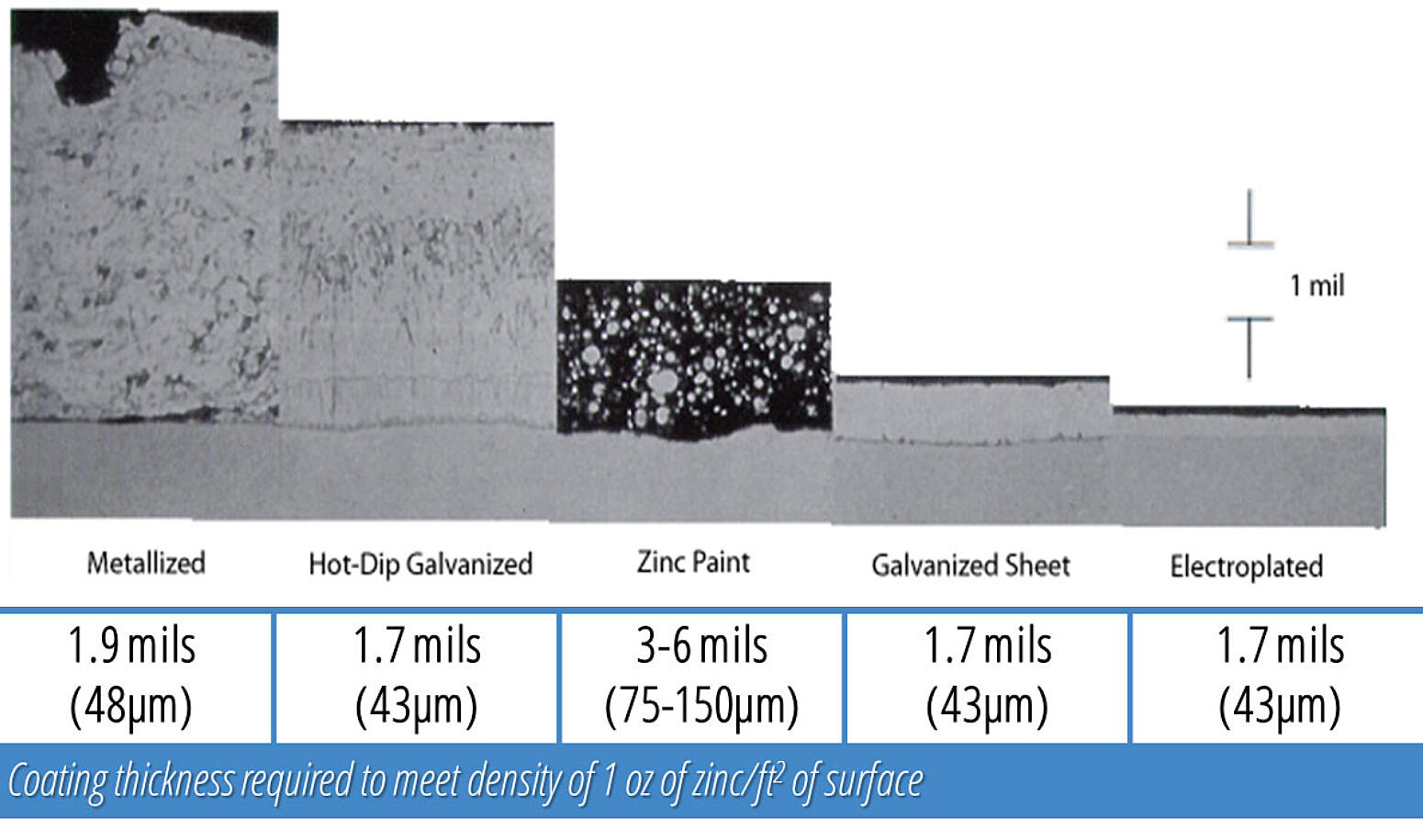
Above is a photomicrograph of various zinc coatings. It depicts the various coating thicknesses and densities of zinc coatings. Refer back to this photomicrograph as you examine the different zinc coatings below.
Metallizing (Zinc Thermal Spray)
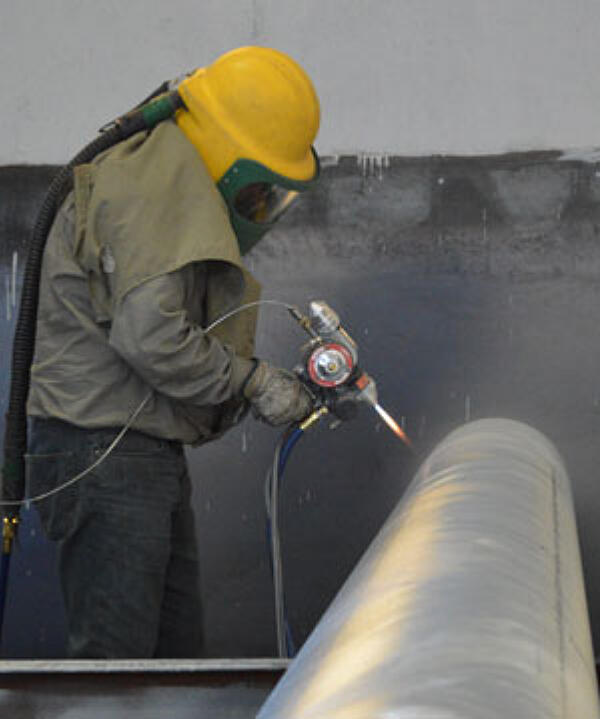
The first coating depicted on the photomicrograph is metallizing. Metallizing or zinc spraying is accomplished by feeding zinc in either wire or powder form into a heating gun, where it is melted and sprayed onto the steel using a combustion of gasses and/or auxiliary compressed air to provide the necessary velocity. Metallizing can be done in the shop or field, is suitable for pieces too large for galvanizing, and is also an acceptable method of touch-up or repair of galvanized parts.
Metallizing (or zinc spraying) coating consistency depends on operator skill, and coating variation is always a possibility. Coatings may be thinner at corners and edges. Metallizing does provide cathodic protection, although there are no zinc-iron alloy layers. Metallizing is only 85% as dense as hot-dip galvanizing, and has a lower bond strength as it is a mechanical bond. So although a thicker coating may be applied, there is actually less zinc present. The black areas on the photomicrograph are the voids in the coating.
Hot-Dip Galvanizing
The properties of hot-dip galvanizing will be discussed in the subsequent sections, but it is important to note the denseness of the coating in comparison to the other zinc coatings. Also, remember hot-dip galvanizing is metallurgically bonded to the steel on the order of about 3600 psi.
Zinc-Rich Paint
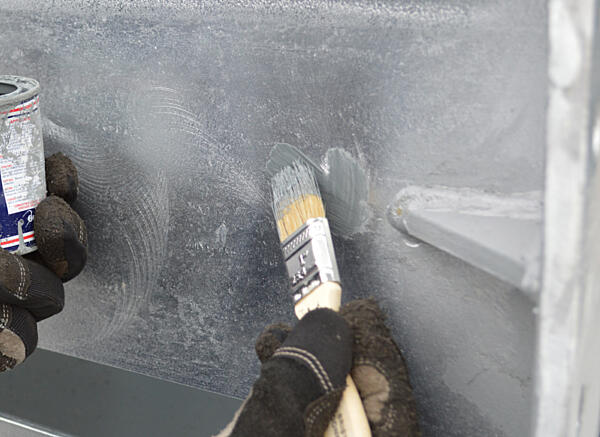
The third coating on the photomicrograph is zinc-rich paint. Zinc-rich paints consist of zinc dust and either organic or inorganic binding material. Zinc-rich paint is often erroneously referred to as cold galvanizing, but zinc-rich paints characteristics and corrosion performance are very different from hot-dip galvanizing. Do not be fooled by claims of similar performance, which are based on salt spray testing. Salt spray tests do not accurately portray real-world conditions, and thus cannot accurately predict the performance of hot-dip galvanizing, which requires the natural wet and dry cycles to form the zinc patina, the critical component of galvanizings longevity.
Unlike other paint coatings, zinc-rich paints may exhibit limited cathodic protection; however, cathodic protection is only afforded if the binding material is conductive, or the zinc particles are in contact with each other and the steel. In the photomicrograph, the gray represents the zinc particles, and the black area is the binding material. Zinc-rich paints are also an acceptable touch-up and repair method for damaged galvanized coatings.
Continuous Sheet Galvanizing
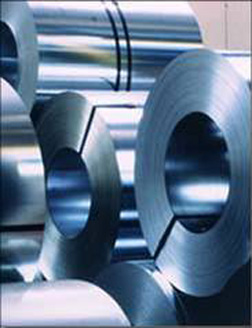
Continuous sheet galvanizing is often confused with after-fabrication hot-dip galvanizing. Both processes involve dipping steel in a tank of molten zinc, but in the continuous sheet process, the sheet metal is fed rapidly through the zinc, and thus picks up a minimal coating compared to hot-dip galvanizing.
The most commonly specified galvanized sheet steels are G60 and G90. The numbers represent the weight of zinc per total surface area for both sides of the steel sheet. So, a G60 coating has about 0.30 oz/ft2 of zinc or approximately 0.54 mils per side. Continuous galvanizing, like hot-dip galvanizing, does provide cathodic and barrier corrosion protection, and has minimal zinc-iron alloy layers.
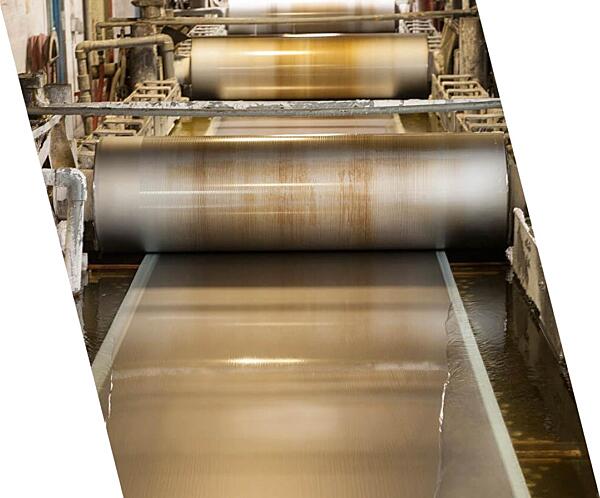
Electroplating
Electroplating (or Electrogalvanizing) generally refers to zinc coatings applied to steel sheet and strip by electrodeposition in a steel mill facility.
There are no zinc-iron alloy layers, however, barrier and cathodic protection is provided. These coatings are very thin and mainly used for interior applications.
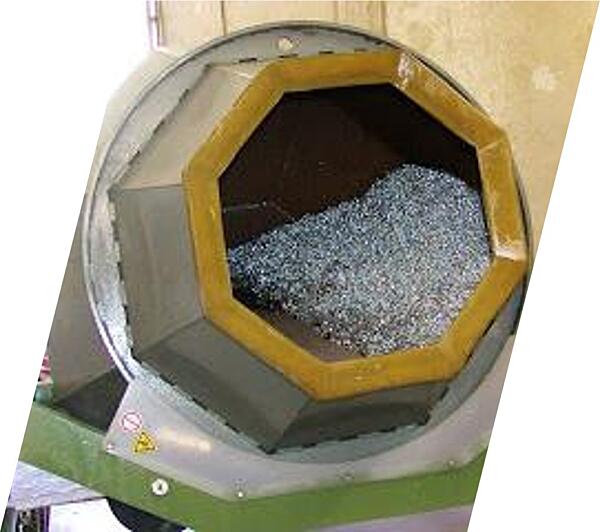
Zinc Plating
One final zinc coating, not depicted on the photomicrograph, is zinc plating. Zinc plating is similar to electroplating, but is used on small parts and fasteners. The parts are tumbled in a drum with zinc powder, proprietary chemicals, and glass beads. The glass beads peen the zinc onto the parts. It creates a mechanically bonded coating, and the thickness is regulated by the amount of zinc in the drum and the tumbling time. However, coating thickness may not be even, and difficult to reach corners and threads may not be coated completely.