Batch Hot-Dip Galvanizing (HDG)
Hot-dip galvanizing produces a protective zinc coating by completely immersing the steel in a kettle filled with molten zinc (Figure 1). Prior to immersion in the zinc bath, the steel is chemically cleaned to remove all oils, greases, soil, mill scale, and oxides. The surface preparation consists of three steps: degreasing to remove organic contaminants, acid pickling to remove scale and rust, and fluxing, which inhibits oxidation of the steel before dipping in the molten zinc. After surface preparation, the steel is immersed in the molten (830-850 F) zinc bath. While in the galvanizing kettle, the molten zinc metallurgically reacts with the iron in the steel to form a durable and uniform corrosion resistant coating containing several layers harder than the base steel and a malleable outer layer of pure zinc.
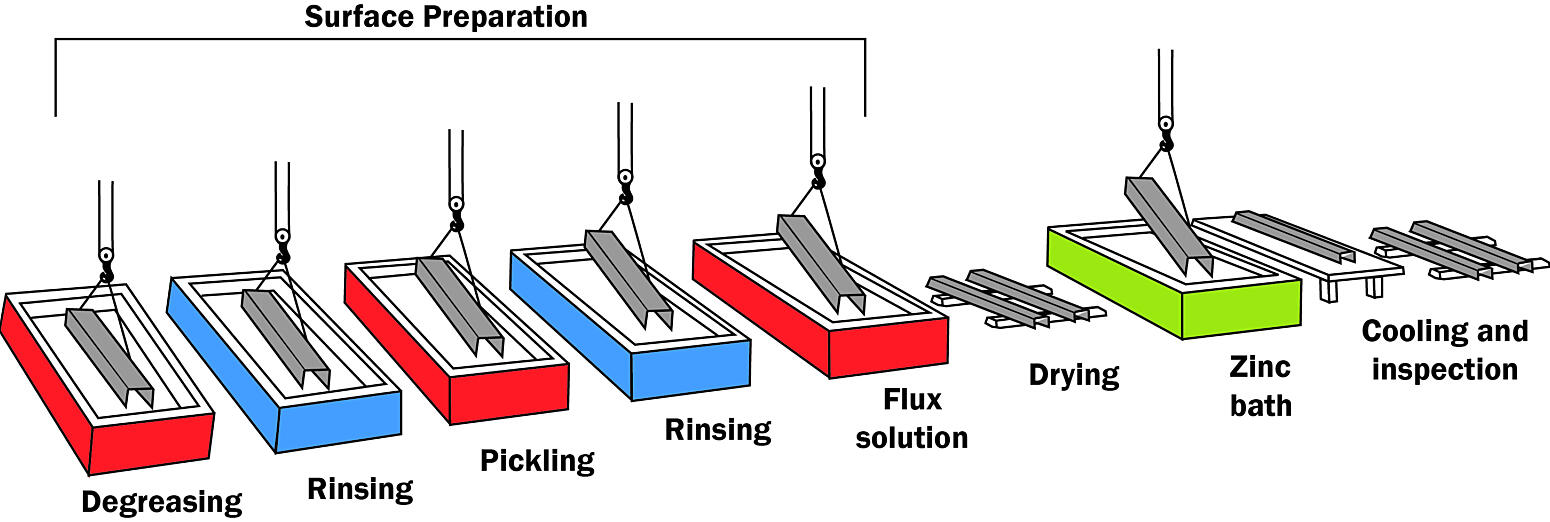
Initial Appearance
It is common for batch hot-dip galvanized steel to have a variety of different initial appearances, including bright and shiny, matte, spangled, mottled, or mixed (Figure 2). These differences can occur between individual pieces and even between sections of the same piece. The initial appearance of hot-dip galvanized steel is difficult to predict and control for a variety of reasons, including steel chemical composition, stress induced during steel processing, and cooling rates after galvanizing.
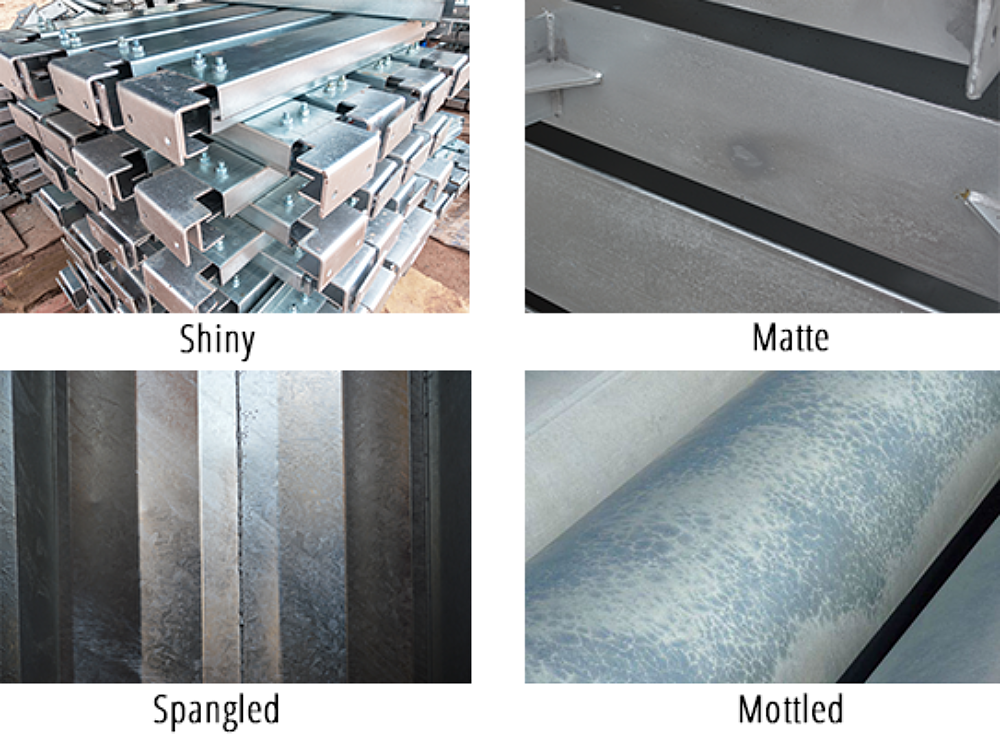
Natural Weathering
Regardless of the initial appearance, all galvanized steel parts will take on a uniform matte gray appearance upon exposure to the environment, typically within six months to two years depending on the exposure conditions. As the coating is exposed to natural wet/dry cycles, it develops a protective zinc patina; the result is a soft and weathered gray appearance - evening out many differences in initial appearance that may have existed originally (Figure 3). Conversely, interior AESS installed in a climate controlled area will not experience weathering, and the initial appearance is unlikely to weather significantly over time.
Post Treatments
Post treatments may be applied to batch hot-dip galvanized steel to assist with rapid cooling of the steel (quenching), passivation of the zinc surface to prevent formation of wet storage stain, or alter the appearance of the zinc coating. For most AESS projects post-treating or quenching galvanized steel is avoided when additional smoothing and/or painting is required after galvanizing. It is important to inform the galvanizer when specifying AESS on a project so they can avoid post treatments that can hinder additional surface treatment after galvanizing. Some post treatments may be intentionally applied to the galvanized surface to produce an alternative appearance. Passivation treatments are available that dull or create an attractive sheen to the surface of the galvanized steel, as well as secondary coatings in a traditional duplex system. A zinc-phosphate conversion coating can be applied to prematurely dull the coating when reflectivity of the zinc coating is a concern. Other proprietary color passivation treatments can be applied that augment the natural finish of the galvanized coating with a specific color.
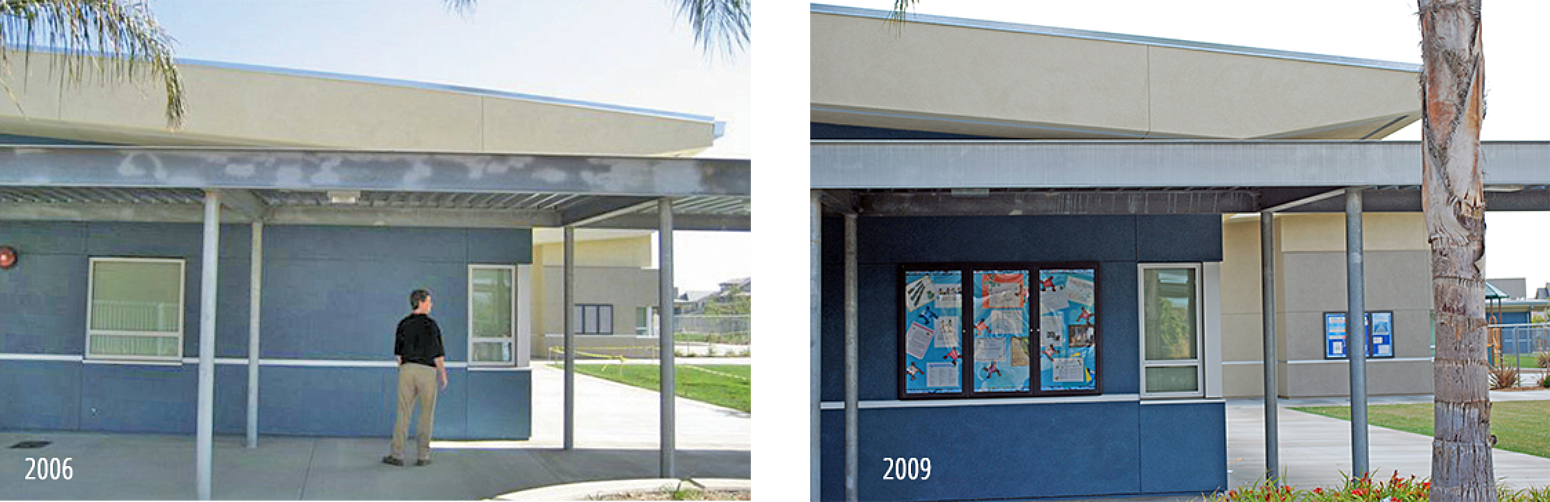
Duplex Systems: Painting or Powder Coating HDG
In addition to post treatments, paint or powder coatings can be applied to hot-dip galvanizing to achieve a desired color. In addition to a specified aesthetic, duplex systems provide improved longevity, 1.5 to 2.3 times the combined lifetimes of both systems, as the result of a synergistic effect between the coatings. Almost any liquid coating system can be applied over hot-dip galvanized coating, but the alkaline nature of the galvanized surface requires a tie coat to be specified for oil-based coatings such as alkyds to avoid saponification. When preparing hot-dip galvanized products for painting or powder coating, surface preparation is critical to the appearance and overall performance. The following surface preparation standards (and choices from the methods presented within), should be specified to clarify the steps necessary to prepare the galvanized surface for painting or powder coating:
- ASTM D6386 Practice for Preparation of Zinc (Hot-Dip Galvanized) Coated Iron and Steel Products and Hardware Surfaces for Painting
- ASTM D7803 Practice for Preparation of Zinc (Hot-Dip Galvanized) Coated Iron and Steel Products and Hardware Surfaces for Powder Coating
The coating manufacturer should be consulted for the best practice regarding application of their coatings over hot-dip galvanizing and the variety of preparation methods presented in ASTM D6386 or ASTM D7803. Although sanding and filing shall be performed to smooth high spots in the galvanized coating, it may also be desired to fill low spots or indentations. To achieve a smooth, paintable surface in these areas and meet AESS category 3 or 4 characteristics, specify a filler material such as caulk or putty be applied by the paint applicator. The coating manufacturer should be consulted regarding compatibility of the filler with the coating to be applied.